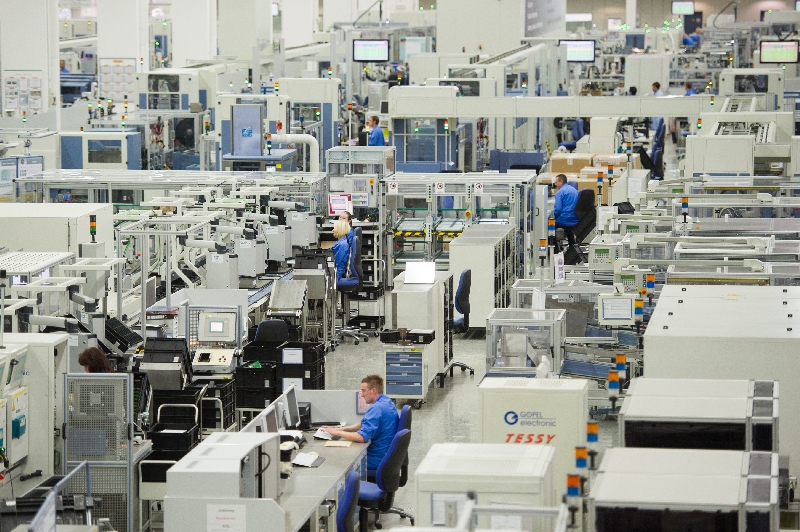
O futuro da indústria já começou, e acontece dentro de um insuspeito prédio de tijolos aparentes, numa pequena cidade do sul da Alemanha. É na fábrica de componentes eletrônicos de Amberg, na Baviera, que a Siemens põe à prova o que alguns chamam de "quarta revolução industrial" ou "indústria 4.0".
Essa etapa eleva a um novo patamar o processo de automação, que em fins dos anos 1960 desencadeou a terceira revolução industrial. Se antes as máquinas mais avançadas eram capazes de fazer algumas funções sozinhas, na indústria digital elas conseguem se comunicar umas com as outras e até com os produtos que passam pela linha de produção.
Na fábrica de Amberg, conhecida na Siemens pela sigla EWA, cada componente carrega desde o início um código que, escaneado, informa como aquele item deve ser fabricado. Como os robôs "conversam" com os vizinhos, a próxima estação da linha logo é avisada sobre o que terá de fazer. Assim, o processo ganha velocidade e fica menos suscetível a erros. Enquanto isso, os funcionários de carne e osso abastecem as máquinas com insumos e checam se está tudo em ordem.
Fábricas de outras empresas na Alemanha, nos Estados Unidos e na China fazem o mesmo, em maior ou menor escala. O que torna a EWA diferente é que nela são produzidos os mais de mil dispositivos do Simatic, sistema de automação industrial da Siemens que equipa algumas das linhas de produção mais avançadas do mundo entre elas, as que já têm um pé na quarta revolução industrial. Não por acaso, o sistema que controla a fabricação do Simatic é o próprio Simatic.
"Um Simatic pode produzir um BMW. Mas um BMW não pode produzir outro BMW", brinca Karl-Heinz Büttner, diretor da EWA, referindo-se a um dos principais clientes da Siemens. Fabricado em Amberg há 25 anos, o sistema vem sendo atualizado desde 1959, quando saiu a primeira versão.
Conceito
Equipamentos e produtos inteligentes são a face visível do conceito de indústria 4.0. Por trás deles está o uso exaustivo de ferramentas de tecnologia da informação, da internet à computação em nuvem, que logo permitirão simular tudo no ambiente virtual, de uma peça à fábrica inteira. Planejar, desenvolver, testar e lançar um produto ficará mais rápido e fácil.
Atualizar linhas de produção e fabricar ao gosto do cliente também tende a ser mais simples, abrindo espaço a uma verdadeira "customização em massa" hoje, mesmo na EWA, as linhas são pouco flexíveis. Mais adiante, supõe-se, o sistema fabril se organizará quase sozinho, com mínima intervenção humana. Uma possibilidade fascinante e, também, um tanto assustadora.
A indústria 4.0 e seus sistemas "ciberfísicos" ainda estão ao alcance de poucos. Mas a contrapartida parece compensar o custo. Segundo a Academia Nacional de Ciência e Engenharia da Alemanha (Acatech), as novas tecnologias devem elevar em 30% a produtividade da indústria local, que já é das mais altas.
A fábrica de Amberg dá uma ideia do que a automação pode fazer. Sua produção anual aumentou oito vezes desde 1989, muito embora o tamanho da fábrica (10 mil metros quadrados) e o número de funcionários (1,1 mil) permaneçam os mesmos daquela época.
Abismo
No Brasil, máquinas têm 17 anos de uso. Na Alemanha, quatro
A automação industrial ficou "sexy" novamente. Quem diz é o executivo-chefe da divisão de indústrias de processos da Siemens, Peter Herweck. Segundo ele, o futuro da manufatura voltou a ser importante não só para empresas, mas também para governos.
O Brasil que o diga. Patinando há anos, nossa indústria produz hoje o mesmo que antes da crise de 2008. E, fora uma ou outra exceção, parece distante do nível 4.0. Basta observar a idade dos equipamentos: em média, 17 anos de uso, segundo a Associação Brasileira da Indústria de Máquinas (Abimaq). Nos Estados Unidos, a idade média é de sete anos e na Alemanha, quatro. "É uma diferença gigantesca de precisão, de produtividade", diz Carlos Pastoriza, presidente da Abimaq.
Modermaq
Segundo ele, a culpa do atraso "do portão da fábrica para dentro" é do que ocorre "do portão para fora". "Anos de real valorizado, taxa de juros elevada, falta de infraestrutura, alto custo logístico, sistema tributário maluco. Nossa indústria ficou com margem quase zerada e parou de investir", diz.
As compras de bens de capital, que já não empolgavam, caíram a níveis alarmantes neste ano. Conforme a Abimaq, o investimento até julho foi 15% menor que no mesmo período de 2013.
A entidade propôs ao governo um programa chamado Modermaq, para estimular a troca de equipamentos com mais de 20 anos, que são 30% do parque fabril brasileiro. A ideia é que o governo dê um crédito fiscal de 15% do valor da máquina nova, a ser financiada por um programa específico do BNDES, e permita a "depreciação superacelerada" do bem um mecanismo contábil que reduz o imposto de renda das empresas.
O objetivo da Abimaq, claro, é fomentar a compra de equipamentos nacionais. "Mas o programa pode abranger também os importados, com a diferença que eles não teriam financiamento do BNDES", diz Pastoriza. Segundo ele, o governo gostou da ideia e, caso reeleito, pode anunciar o programa logo após as eleições.