Ouça este conteúdo
Por todo lugar que se vá dentro das fábricas da Renault no Paraná, no Complexo Ayrton Senna (CAS), em São José dos Pinhais (município da Região Metropolitana de Curitiba), é impossível não se deparar, em algum momento, com algum veículo autônomo, ou Automatic Guided Vehicles (AGV, na sigla em inglês). São mais de 230 deles em circulação nas quatro unidades de produção do CAS, o que os torna um dos fatores mais visíveis da quarta revolução industrial presente na unidade - a chamada “Indústria 4.0”.
Essas máquinas inteligentes trafegam durante todos os turnos de produção, fazendo o transporte de peças e de ferramentas em rotas programadas e controladas, de forma que cada um dos operadores tenha à mão tudo o que precisa para montar, em todos os detalhes, cada um dos oito veículos fabricados no CAS.
Esta tecnologia é apenas uma dentre tantas outras que conferiram à fábrica paranaense da Renault o reconhecimento do Fórum Econômico Mundial (WEF), em 2020, como Advanced 4th Industrial Revolution (4IR) Lighthouse – Farol da 4ª Revolução Industrial Avançada. O CAS é a única planta industrial instalada no Paraná, e uma das duas únicas na América Latina, a receber tal certificação.
Integração digital da venda à fabricação dos veículos na Renault do Paraná
Mas, afinal, de que forma a indústria 4.0 está presente nas fábricas da Renault no Paraná? Quem respondeu a essa e a outras perguntas foi o gerente industrial da marca para a América Latina, Fabiano Silva. Ele acompanhou a visita da reportagem da coluna Paraná S.A. ao CAS da Renault no Paraná e explicou que essas tecnologias e processos digitais foram adotados na unidade desde o início do processo de fabricação dos veículos até a venda ao consumidor final.
O processo de integração digital tem na venda online um de seus pontos cruciais, de acordo com o gerente. “Hoje é possível que um cliente nosso compre um carro pelo celular ou pelo computador, como qualquer outra compra digital. E esse processo é completo, vai desde o financiamento, pré-avaliação do usado, até a geração dos boletos de pagamento. É uma solução voltada para esse perfil de consumidor mais conectado e atrelado às soluções digitais”, disse ele.
O Kwid é um dos carros fabricados em São José dos Pinhais. Mas, como explicou Fabiano Silva, não é apenas um veículo: opções de customização de motorização, opcionais e acabamentos disponíveis aos clientes dão um total de mais de 50 combinações diferentes. E a fábrica precisa estar pronta para atender a cada uma dessas customizações, não só para o modelo, mas também para o Sandero, o Stepway e o Logan, disponíveis para compra online.
Peças são rastreadas da fabricação à montagem no carro
Logo na entrada da fábrica CVP (Curitiba Veículos de Passeio), uma grande máquina chama a atenção. É uma prensa, responsável por cortar as chapas de aço nos formatos de cada uma das partes da carroceria dos veículos. Seria algo comum em uma fábrica de carros, até mesmo pelo barulho produzido pelo equipamento. Mas é aqui que começa o processo de rastreabilidade interna de cada uma dessas partes, necessário para que elas cheguem até os postos de soldagem.
“O sistema é todo integrado, e é essa integração que nos permite atingir a marca de um carro saindo a cada minuto da linha de produção. Começa com cada uma dessas peças, passa pela soldagem, pela pintura, pela montagem e checagem final. Cada uma dessas partes tem um caminho predefinido a partir de agora, que é o carro, no modelo e na cor que o nosso cliente escolheu”, disse Silva.

E é justamente a bordo daqueles veículos autônomos inteligentes que as peças seguem para a soldagem, uma das muitas etapas de fabricação feitas por robôs. Em uma espécie de balé tecnológico, as partes são unidas pelas soldas precisas das máquinas, orientadas por um sistema de dados interligado ao sistema geral da fábrica. Uma vez pronta, as carrocerias são transportadas por esteiras até o processo de pintura.
Em outro ponto da linha de produção, os motores – cujos bloco e cabeçote são feitos na CIA (Curitiba Injeção de Alumínio) e montados na CMO (Curitiba Motores) – ganham vida pelas mãos ágeis de operadores humanos e robôs colaborativos. As máquinas aqui não só não substituem o trabalho das pessoas como ajudam a tornar o processo mais rápido e seguro. “Esses robôs colaborativos são uma peça-chave nessa etapa. A eles cabe realizar funções que para as pessoas seriam menos ergonômicas ou que exigiriam muita força braçal”, confirmou Silva.
Inteligência artificial aprende e ensina robôs dentro do complexo industrial
Ao final desta etapa, uma outra estrutura robótica cumpre papel primordial na linha de produção. À primeira vista, como definiu o gerente industrial, não é algo que chame muito a atenção, para um observador desatento. Mas as câmeras instaladas nas pontas de longos braços mecânicos alimentam um sistema de inteligência artificial (IA) que identifica qualquer não conformidade no motor já montado.
Esses dados, informou Silva, são retroalimentados junto aos robôs colaborativos para que esses façam, quando necessário, pequenos ajustes no processo de trabalho. “Se uma peça ficou com uma fixação alguns milímetros fora do que deveria, o próprio sistema de IA passa isso para o robô colaborador, que ‘reaprende’ a fazer o trabalho. Tudo isso sem nenhuma interação humana”, disse.
Operadores têm acesso a sistema integrado com gestores na linha de montagem
Montadas no chassi, todas as partes da unidade motora se unem à carroceria em um processo que leva menos de 60 segundos. A partir desse momento, o carro segue para outra esteira, onde são instalados os para-choques, faróis e lanternas traseiras. Nesse ponto da linha, Silva chama a atenção para pequenas telas instaladas ao lado do posto de trabalho dos operadores. Além de ter à mão informações sobre o modelo que está sendo montado no momento, por esse sistema é possível acionar os líderes do setor, que são notificados em seus tablets, também interligados à toda a rede de dados da fábrica.
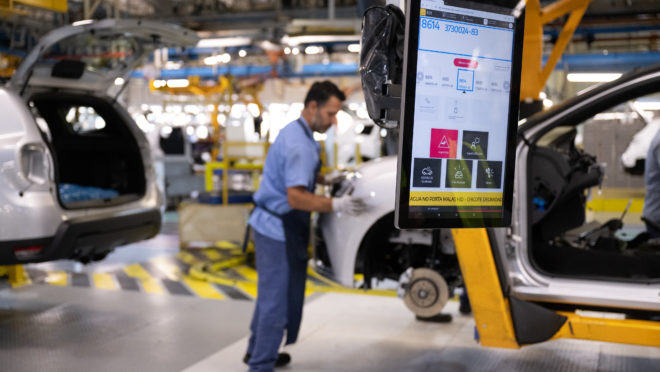
“Esses tablets permitem a cada um dos supervisores e chefes de produção visualizar o fluxo da fábrica em tempo real. O sistema dá mais autonomia aos operadores e mais capacidade reativa a esses líderes. E os dados gerados podem ser consolidados até mesmo com a nossa área comercial, assim como com a cadeia de fornecedores. O ponto ideal, que nós buscamos, é não ter estoque. Parece estranho, mas estoque é recurso parado. Com esse sistema, nós conseguimos nos aproximar disso, de poder dar a ordem de fabricação das peças conforme elas estão sendo instaladas nos carros”, comentou Silva.
Já no fim da linha de produção é feita a última inspeção visual da pintura e do acabamento dos carros. Este trabalho meticuloso e detalhista é feito por operadores altamente treinados. Como explicou o gerente industrial, mesmo os sistemas mais avançados não se comparam ao tato e à visão de um bom operador.
“Não é nem nunca foi nosso objetivo substituir pessoas por máquinas, simplesmente pela troca em si. Nós queremos nossos operadores concentrados em trabalhos nobres, e não realizando tarefas simples como puxar ou empurrar carrinhos. É para isso que usamos a tecnologia, para melhorar o trabalho”, definiu.
Sistema interno de rastreamento inteligente diminuiu em 30% tempo de expedição dos carros
Por fim, os carros ganham vida ao serem ligados pela primeira vez. Na sequência, cada veículo passa por mais uma série de testes antes de seguir para o pátio ou direto para os caminhões cegonha com destino ao Porto de Paranaguá. E como saber para onde vai cada um dos carros que sai a cada minuto da linha de produção? Fabiano Silva tem a resposta.
“Utilizamos um sistema de identificação por radiofrequência (RFID), também interligado ao sistema de dados do complexo, que nos permite identificar onde está e para onde vai cada veículo feito tanto aqui na unidade de carros de passeio quanto na fábrica de utilitários. Com esse sistema de rastreabilidade, conseguimos reduzir em 30% o tempo de expedição dos nossos veículos. Na prática, o carro chega mais rápido nas mãos do cliente”, explicou.
O sistema de rastreamento, garante o gerente, não funciona fora da fábrica da Renault no Paraná. Mas, no futuro, o RFID pode ajudar o cliente que fez o processo de compra digital de um carro acompanhar, em tempo real, cada uma das etapas da fabricação, desde a moldagem das chapas de aço até o embarque para as concessionárias. “A tecnologia para tanto já existe. Se nós percebermos que isso pode ser algo importante para o nosso cliente, por que não estudar a possibilidade de implementação? Seria um passo a mais na digitalização desse processo, literalmente desde a compra até a entrega do carro zero”, ponderou.